Stored energy in a system is the biggest potential hazard when any work is required on plant and machinery. Energy is often only considered as Electrical but is often in other common forms such as:
- Pneumatic – air pressure in lines and receiver
- Hydraulic – in hoses and pressure held by safety fuse
- Potential – rocks in a bucket on a conveyor
In most cases this work is carried out by maintenance engineers and contractors but very often the same hazards are exposed to operators and cleaners during unplanned breaks. This stored energy can of course cause a sudden unplanned movement of the equipment during the works which can then result in a near hit in the best outcome and in the worst case a life-changing injury of fatality.
Safe isolation of these energy sources from causing such an incident is a legal obligation and covered under the UK regulations below:
- Health and Safety at Work etc. Act 1974
- Management of Health and Safety Regulations 1999
- Electricity at Work Regulations 1989
- The Provision and Use of Work Equipment Regulations 1998
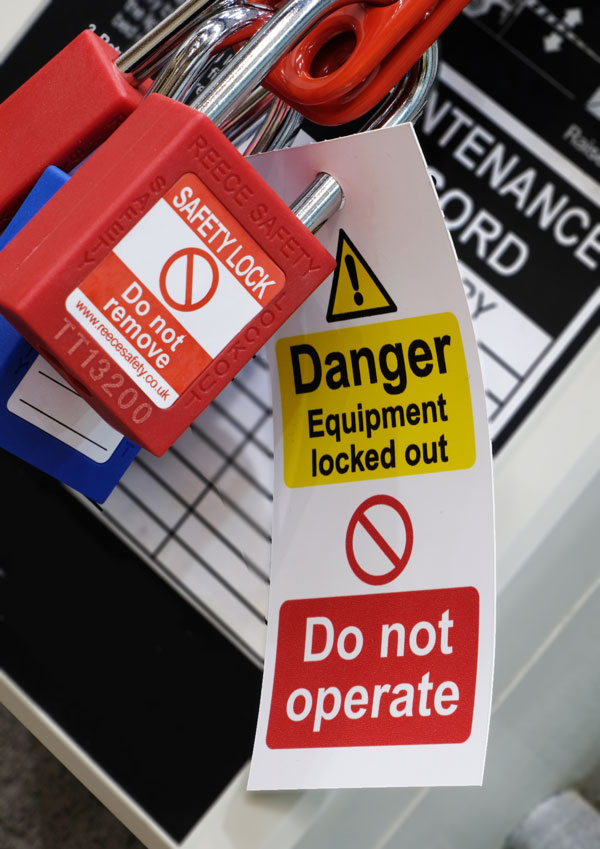
A commonly used acronym now being adopted is LOTOTO which is Lock Out – Tag Out – Try Out. This effectively describes the process where the energy isolation is initially LOCKED to prevent accidental or unauthorised re-energisation. The locking device is then TAGGED to show who is working on it and to warn others. Finally, the equipment is then tested to try and turn on with local isolators and switches – this TRY OUT will show if an unexpected secondary energy source is present or if there is a defective isolator.
The common belief of a Safe Isolation system is that it will slow down the work and reduce output. Whilst nobody would consciously put others in harm’s way the pressure for output in a company can create bad habits and shortcuts. Most companies have never had a bad accident before a major incident occurs due to a shortcut. A well thought through safe system of work with the correct isolation equipment will fit in quickly with normal operations and very soon seen as the only way to work. Many systems set up with bad selection of equipment bought merely to achieve legal compliance will often lie idle in the workshop and not used unless under sufferance.
Keeping the isolation equipment on or near the isolation point is a winning strategy and very often a bespoke lockout station will be used to make sure that the equipment is always present and obvious to any supervision that it is missing. Localised lockout stations are now seen as the way to go and when branded with corporate colours fit in well with the Corporate message of “Safety First!” or “Zero Harm”.
Engraved safety padlocks with names and lockout tags with photographs have been proven to be used in a more considered manner than “anonymous” equipment – “one man; one lock” is the commonly used phrase. People putting their name to something have a stronger ownership and accountability to both the job and looking after their own equipment. This approach is fast becoming the best practice in successful isolation systems. Modern plant often requires multiple people to repair or clean the equipment and a simple system for Group lockout will eliminate the risk where the “last man; last lock” principle makes sure all people are safe before the re-energisation takes place.
A final consideration mentioned previously is with Contractors and Cleaners who are often forgotten about when designing a safe isolation system. A separate set of locks readily available to be issued in a controlled manner to each person achieves the “one man; one lock” principle on a temporary basis and making someone sign the equipment back in will prevent loss of this equipment. Whilst this separate system is required to allocate the safety padlocks they can then fit into the normal safe system of work with the issued padlocks.
Contractors introduce different risks as in many cases the responsibility of who should isolate is a grey area. A contractor’s RAMS isn’t often enough to guarantee isolation is performed as per the corporate standard and what would happen if they don’t bring their own lockout equipment? As the contractor is working on your site the provision of your equipment for use by contractors is now seen as the safest solution.