Everyone working with electricity should be wearing insulating gloves to protect them from the danger of electrical shocks and burns – it can be a matter of life or death. The hands are extremely susceptible to this risk because they are usually the first point of contact in terms of exposure to high-voltage currents. Even minor electrical shocks can be fatal if someone has an unknown heart condition.
No matter where or what the industry or environment, from live electrical working/testing through to automotive, Lock Out Tag Out Try Out (LOTOTO) and arc flash hazards, electrical insulation gloves (also known as electrician gloves, insulating rubber gloves, electricity gloves and linesman gloves) are essential wear to keep people safe at work. They also provide important benefits like enhanced grip and protection against abrasion and cuts.
Electrical insulation gloves manufactured to EN60903 and ASTM D120 Standard Specification for Rubber Insulating Gloves are tested to ensure the highest performance levels, combining high levels of dielectric strength, durability and comfort.
The importance of electrician gloves for electrical workers
Insulating gloves are integral to any safety programme for electrical workers, providing effective protection against extended contact with energised conductors and other equipment.
- Today’s advanced electricity gloves are manufactured using non-conductive materials such as silicone and rubber, often used in conjunction with leather overgloves. The resultant high dielectric properties mean they provide effective protection against the hazards of electric shock and burns.
- There are strict regulations set by Health and Safety bodies such as the HSE governing the style, care and use of electrical insulation gloves, which are classified based on several properties and voltage protection – more on this later in this blog.
- The right insulating gloves provide effective protection against shock and burns, cuts and abrasions from sharp objects, better grip on tools and equipment and compliance with important health and safety regulations.
- Choosing the right pair of gloves for the task at hand is vital, in terms of material and protection levels and regulatory compliance. The correct fit is vital too.
At Reece Safety, we supply an extensive range of fully tested electrical insulation gloves designed for every level of voltage and arc flash protection.
Take a look too at the Reece Safety free guide to the Storage and useful life of Electrical Insulating Gloves, which covers recommendations for storage, checking, periodic inspection and cleaning.
Selecting the correct electrical gloves
When choosing electrical safety gloves, the following criteria should be considered.
Standards and working voltage protection (Class)
Insulating electrician gloves used in Europe must comply with EN 60903 standard Electrical Insulating Gloves. This rigorous standard covers all aspects of glove performance including dielectric properties, characteristics such as composition and dimensions, tensile strength, resilience to puncture and thermal properties. Resistance to ozone and other substances may also be specified.
EN 60903-compliant gloves are defined by six classifications, relating to the voltage they are capable of providing electrical shock protection against. These are as follows:-
Class 00 – 500 volts AC 750 volts DC
Class 0 – 1,000 volts AC 1,500 volts DC
Class 1 – 7,500 volts AC 11,250 volts DC
Class 2 - 17,000 volts AC 25,500 volts DC
Class 3 - 26,500 volts AC 39,750 volts DC
Class 4 – 36,000 volts AC 54,000 volts DC
The ASTM label system
The ASTM label system uses colour to define immediately and visually the voltage protection level for each classification and carries information including the manufacturer/brand, country of origin and maximum voltage protection.
Class 00 – Beige
Class 0 – Yellow
Class 1 – Red
Class 2 - White
Class 3 - Green
Class 4 – Orange
Insulating material
Electricity gloves are available manufactured from latex, leather and composites. Reece Safety offers a comprehensive range with an appropriate pair of gloves to match all voltage requirements.
Natural rubber latex
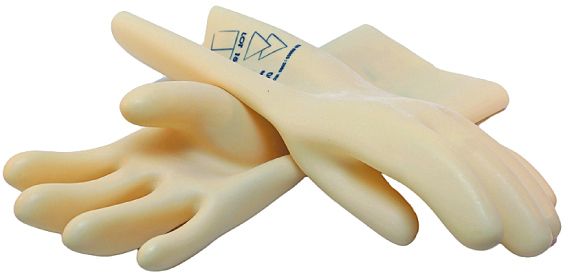
Fully insulating natural rubber latex construction gloves provide high dielectric characteristics, and an ergonomic shape and are easy to put on and remove. The latest insulating glove designs feature the thinnest latex construction without compromising insulating properties, which makes it much easier for the user to perform normal functions when wearing the gloves.
Leather
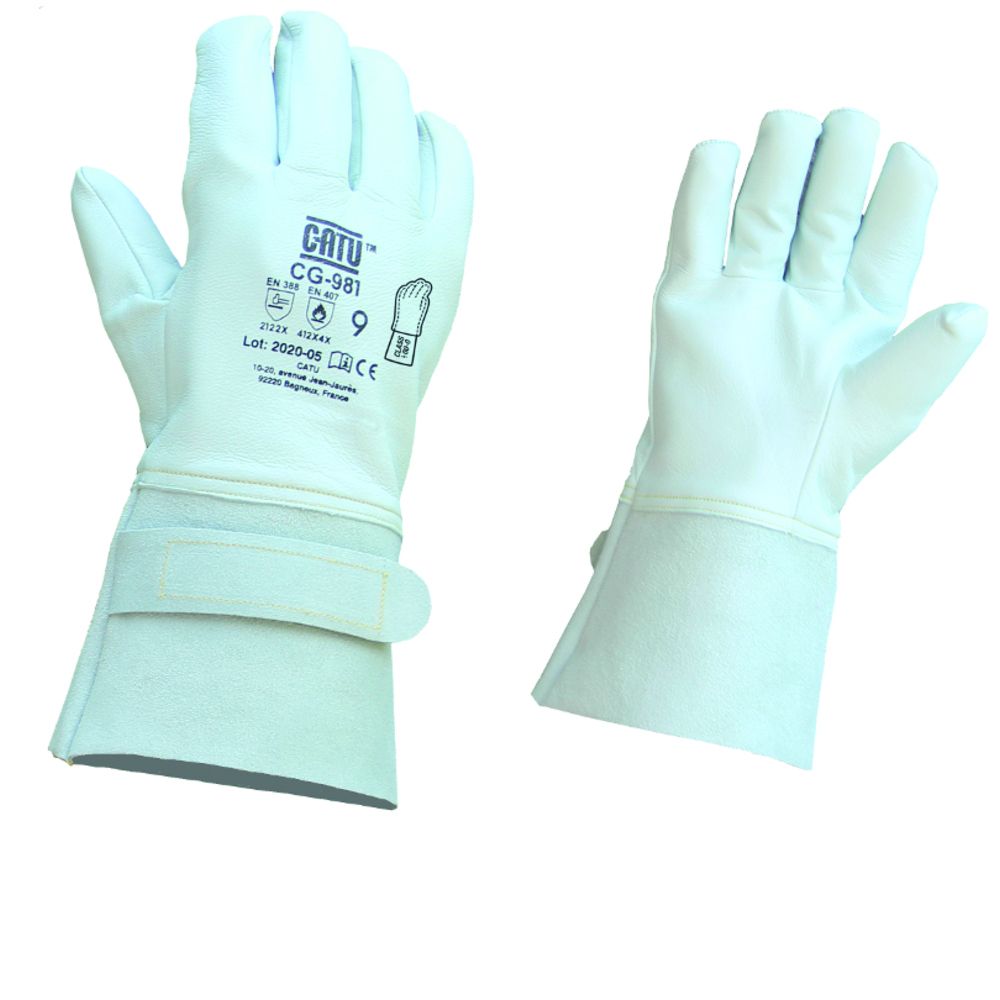
Leather overgloves are used to protect against mechanical damage for latex gloves. The best designs feature supple leather palm areas to improve dexterity, with tough and hardwearing backs for durability.
Composite
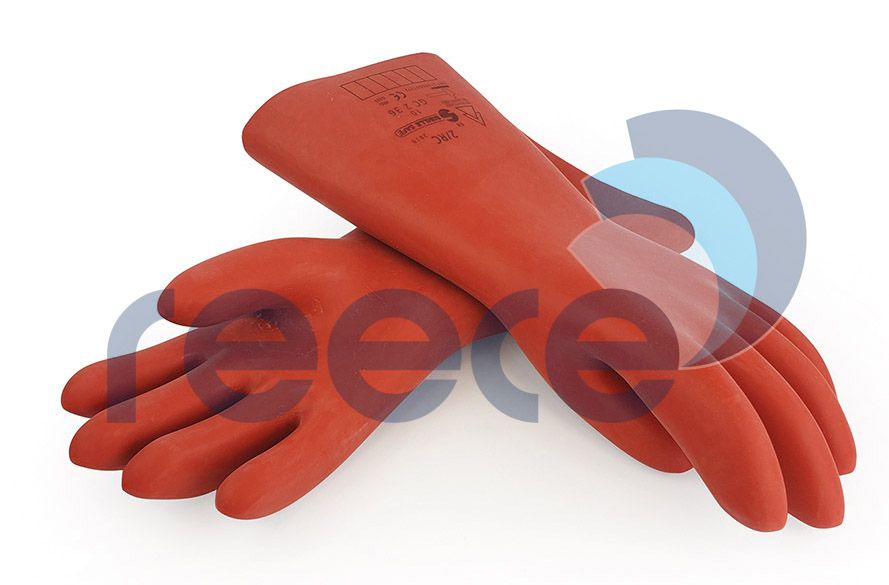
Composite insulating gloves give mechanical protection and puncture resistance through a secondary layer of resistant material, with the base latex layer providing the insulating properties. This means users experience improved levels of dexterity without the need for leather overgloves. Added benefits include excellent grip in humid environments and good mechanical resistance. The tougher construction makes them much more tear resistant too.
The development of composite electrical safety gloves has achieved arc-rated protection, providing a fully electrically insulating glove with mechanical protection and excellent levels of arc-flash protection, variable with the EN 60903 voltage gloves class.
Product Colour
Natural latex electrical insulating gloves are usually produced in beige, which may have a red additive for improved visibility and appearance.
Composite construction gloves from Reece Safety are usually orange and feature a two-layer design, with the outer layer for mechanical strength and the inner layer providing the required level of insulation and electrical safety. The inner layer is usually black; the key benefit of this is if there is a cut or damage to the outer layer, the black layer will show on visual inspection and the gloves should be removed from service.
Size, fit and dexterity
Being able to perform tasks requiring fine motor skills is an essential part of most electrical work, so how the pair of gloves affects dexterity and movement around electrical equipment is an essential consideration when choosing the right insulating gloves.
- Most gloves are available in sizes 7 – 12 to match standard hand sizes, but extra small and extra large options are also obtainable. If they are too big or too small, the greater the chance an electrical worker will be tempted to remove them to complete more intricate work.
- Electrical gloves should be properly fitted for maximum benefit.
- Measure the circumference of your hand at its broadest point and measure from the tip of your middle finger to the bottom of your hand where it joins your arm. The largest of these measurements (in inches) represents your glove size.
- Always check your gloves before you use them. Look for nicks and discolouration. Inflate the gloves to check for air leaks.
- Unscented talc is commonly used with latex gloves for easy donning of the gloves.
Environmental resistance
Be aware of the AHZRC environmental resistance categorisations.
- A – Acid
- H – Oil
- Z – O-Zone
- R – Acid, Oil and O-Zone
- C – Very Low Temperatures
Under or Over Gloves
Many electrical insulating gloves are designed to be used only with overgloves or undergloves.
Over gloves are used for the mechanical protection of latex gloves, protecting the vulnerable latex from nicks and cuts. Any damage to the latex layer could allow moisture ingress and lead to voltage transfer to the hand underneath.
Leather over gloves are available from Reece Safety in two distinct ranges. Over gloves designed for the lower insulating classes are higher grade leather to reduce dexterity loss. Higher-rated over gloves are manufactured using a coarser grade of leather for a tough glove surface, resistant to cuts and damage.
Cotton under gloves are often worn to absorb moisture for greater comfort for the wearer.
Testing of insulating gloves
These gloves are not known to have a defined shelf life and will normally only fail due to mechanical damage in use. They can be safely stored in their sealed packaging for 12 months from manufacture and retested at this point to last another 12 months; this cycle can continue indefinitely. They then need testing every 6 months in use – irrespective of the date of manufacture.
It is now widely accepted that class 0 and 00 gloves simply need a pneumatic test to check for rips and tears. The higher classes will also need a dielectric test using a specially designed glove tester. It is recommended that gloves are given a visual inspection and manually inflated before each use to check for rips. Higher-class gloves must be tested every 12 months, even if they have not been used.
See our useful guide which contains information on re-testing requirements.
Storage of gloves
It is important to store and clean gloves appropriately.
- Store electrical insulating gloves in storage bags in a cool, dry place, cuff side down to prevent ingress of dirt and objects.
- Store under gloves and over gloves separately to ensure both elements of protection are inspected before use.
- To clean, use only tepid water and mild detergents.
Class 0 gloves in automotive workshops
With the increase in hybrid and electric vehicles, class 0 insulating gloves are now becoming the accepted PPE standard in automotive workshops where people working on electrical components need electrical protection with electric gloves capable of protecting against up to 1,500V DC.
Summary
Protecting people against electric shock and burns from electrical equipment is vital when buying protective workwear like electrical insulating gloves. Choosing the right gloves for each application is critical – browse our selection of products to check on performance and suitability.