With working at height commonly acknowledged to be one of the most hazardous tasks undertaken across industry, the Permit to Work system is an important framework to ensure the protection of all those involved, as part of the existing Working At Height Legal Requirements & Guidance legislation.
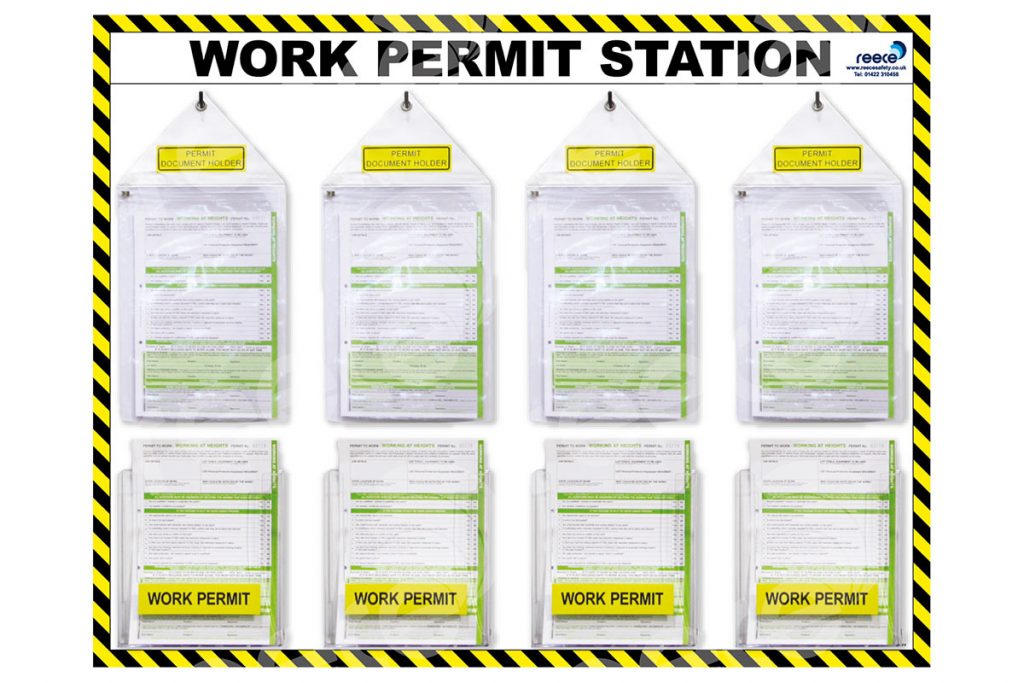
The HSE (Health and Safety Executive) defines a Permit to Work as a formal recorded process used to control work which is identified as potentially hazardous.
Whether you require a Permit to Work when working at height – or in any other potentially hazardous environment such as confined space entry - may depend on the site location or even the contractors involved. The objective is to achieve optimum worker safety.
Permit to Work controls apply to all those involved in the working process, including employers, employees and self-employed individuals. Employers must verify that adequate training has been completed and that required qualifications are in place for safe working practices. They must also ensure that all the necessary equipment and precautions are in place, as well as applying all the relevant controls, restrictions and safety protocols to maintain individual and team safety.
The HSE sets out several key requirements for safe working at height. A Permit to Work is all about recognising and controlling risk, and ensuring all work carried out is planned, supervised and completed by competent people.
The system provides the framework to assess and document levels of competence and experience, defining the parameters of each job in terms of hazards, equipment required and general safety considerations.
Commercial training courses such as those provided by Reece Safety deliver a detailed overview of the permit-to-work systems, where they are required, what a permit should contain and who is responsible for preparation and management.
Reece Safety courses can also combine the requirements for Confined Space management and entry and Height Safety with the PTW training.
Let’s take a more detailed look at the Permit to Work.
What is a permit to work?
Any task defined as high risk or hazardous and subject to a risk assessment, such as hot works, electrical works, working at height and working in confined spaces requires a Permit to Work. It is a written document outlining the work which needs to be completed, where and within what timeframe. It is only valid for one specific task in one environment.
The permit is a vital component of any safe system of work, detailing the precautions which need to be taken, the checks and balances, the equipment required and the levels of competence of the individuals involved. The purpose is to identify all potential hazards and seek to mitigate these before work commences.
It is far more than a piece of paper; it is a defined and written system to ensure risk management is implemented and hazards are properly managed and effectively controlled. The Piper Alpha disaster of 1988, which killed 165 offshore workers and two seafarers, was caused by a flawed Permit to Work system, as summarised in the subsequent report by the Hon Lord Cullen.
This PDF booklet (HSG250) produced by the HSE provides more detailed guidance on the Permit to Work system in the UK.
Who needs a permit to work?
Specific tasks have differing levels of risk, and whether a permit to work is required will be determined by a competent person/responsible person in a position of authority.
Only a competent person in a position of authority can decide if a permit to work is necessary. It is also only within the power of a competent authority figure and the person managing the project to sign off on a permit to work.
The permit to work system plays an important role in accountability, responsibility and safety protocols, communicating vital information on risks and hazards and documenting procedures and instructions to ensure safety across the entire process.
This formally documented process is commonly required in several different environments.
- Working at height – one of the key environments where occupational injuries and accidents occur
- Confined spaces – to authorise entry and investigation in environments such as vessels and tanks, preventing unnecessary risks. Additional permits will be required to conduct work in these spaces.
- Hot work – all tasks relating to fire and heat and fire hazards
- Cold work – a general permit covering chemicals, heavy lifting, scaffolding
- Electrical work – hazard identification, mitigating risk and working in a safe manner
- LOTO or LOTOTO – Lock Out, Tag Out, Try Out – ensuring maintenance, inspections and repair work can be safely carried out without any risk of activating equipment and other assets.
What details will the permit include?
A typical permit to work will cover off:-
- A permit to work reference number for auditing purposes
- Date and time information (the permit must be up to date) and work location details
- The timeframe for the work, which may vary according to industry, environment and application according to the speed of change in terms of risks and hazards
- A description of the work to be carried out with relevant job details to demonstrate consideration of potential risks
- Details of critical risks and hazards with risk assessment references
- Information on equipment required and any safety testing to be carried out as necessary safety measures
- Information on emergency procedures (site-specific)
- Signatures – multiple signatures may be required for different stages of the task.
What is classed as working at height?
In the UK, 138 workers were killed in work-related accidents in 2023/24, and 50 of these deaths were caused by falls from height (Source: Statistics - Work-related fatal injuries in Great Britain)
Typical working at height activities include a wide range of construction industry-related tasks including scaffolding, roof work and even painting and decorating on working platforms. Although there is a common belief that ‘working at height’ covers everything over two metres, in fact for health and safety it can include any occupation or activity where an individual could fall and sustain personal injury.
Working at height therefore includes:-
- Any work undertaken above ground or floor level
- Any work undertaken where an individual could fall off an edge, through fragile surfaces or an existing gap
- Also falls from ground level into openings or holes in floors and grounds
The Work at Height Regulations 2005 is an important piece of legislation here. Communicating risk control measures with all involved is vital, as is ensuring all personnel involved using work equipment and personal protective equipment are competent to do so.
The concept of a ‘competent person’ is vital here across all Permit to Work systems in all environments, not just working at height.
A competent person is an individual who has sufficient training and experience or knowledge and other qualities to enable them to perform tasks safely and to advise others. Competence in Health and Safety is a vital aspect of workplace activities.
The Permit to Work system provides a framework spanning different environments to ensure the risks and legal aspects of individual tasks are fully understood. Any person who is required to issue permits to work as part of their role should consider attending an approved course covering risk assessments, method statements and managing higher-risk activities requiring a Permit to Work.
What are working at height regulations?
Key legislation covering working at height is The Work at Height Regulations 2005, which applies to all tasks carried out at height, regardless of equipment used, the timeframe for the work and the actual height at which the work is to be completed.
Regulation 6 of the Work at Height Regulations 2005 puts the onus on a three-stage approach to minimise the necessity for work to be carried out at height:-
3 Stage hierarchy
- Avoiding working at height wherever possible by completing as much of the task as possible at ground level
- If work must be carried out at height, prevent any falls from occurring
- Ensure the distance and consequences of any falls are minimised using fall protection equipment.
In addition, The Health and Safety at Work etc Act 1974 legally requires employers and employees to comply with health and safety duties and requirements and to take reasonable care of workers and others who may be affected by your actions.
As part of this, it is a legal requirement for employers to ensure that appropriate training is carried out for employees engaged in activities with any element of risk, from working at height to working in confined spaces.
How long does the permit to work last?
Each permit to work issued is pertinent to an identified task and will include information on the timeframe for completion of the task.
In fast-changing industrial and commercial environments, permits may not be valid for more than one day, as the working conditions may change and the risks require assessing again where the permit conditions have altered.
What challenges do employers face with PTW and working at height?
The onus is on employers to comply with regulations and navigate through the rules and regulations to maintain a culture of safety. Permits to Work provide documented evidence to demonstrate that employers are committed to following the correct risk assessment and safety procedures by controlling all risks before work begins.
An effective permit to work system protects individuals against work-related hazards, preventing accidents and injuries, ensuring everyone is on the same page and clearly understands the job to be completed, and communicates risks, hazards and strict safety protocols effectively.
How does Reece Safety training prepare candidates?
At Reece Safety, we offer a range of courses around working at height and working in confined spaces, alongside courses designed to prepare people to issue permits to work in line with relevant legislation.
These include the training of skills, assessment of competence and auditing of performance to support the implementation of the Permit to Work system. The person successfully completing the course would be deemed competent in undertaking your Permit to Work permits.
Corporate approach to PTW
Reece Safety also provides specialist consultancy for organisations wanting to implement an enterprise-wide Permit to Work system, from an initial needs analysis to the design and implementation of documentation.
Where required, this can include establishing a Permit Office where permits are issued and stored, including the control lock boxes, card safes and permit wallets. For shutdowns where numerous different Permits to Work will be required over a defined space of time, Reece Safety can lease out a Portable Permit Office, fully kitted out and ready to plug into mains supply. This helps with the common influx of contractors which can overwhelm the facilities in place to handle normal running operations. If facilities are stretched then shortcuts can be made accidentally.
Electronic Software used for PTW
The Nisoft suite of software tools is a popular choice for Permit to Work systems, integrating with other operations and providing the collection and analysis of data as well as safety processes and record keeping.
Permit to work training
Permit to work training offered by Reece Safety includes:
https://www.reecesafety.co.uk/training-and-consultancy/permit-to-work/
Working at height training
Specific Working at Height training offered by Reece Safety includes:
https://www.reecesafety.co.uk/training-and-consultancy/working-at-height/
There are lots of courses in this section.
In summary
A Permit to Work is required anywhere hazardous, high-risk work subject to risk assessment is carried out. Where significant risks exist, it provides a formalised framework setting out strict conditions and procedures to control risks in workplace environments.
If you need to know more about implementing Permit to Work systems, contact Reece Safety to find out how our training courses are helping the industry to work more safely.